What You Need To Know About High-Speed Machining
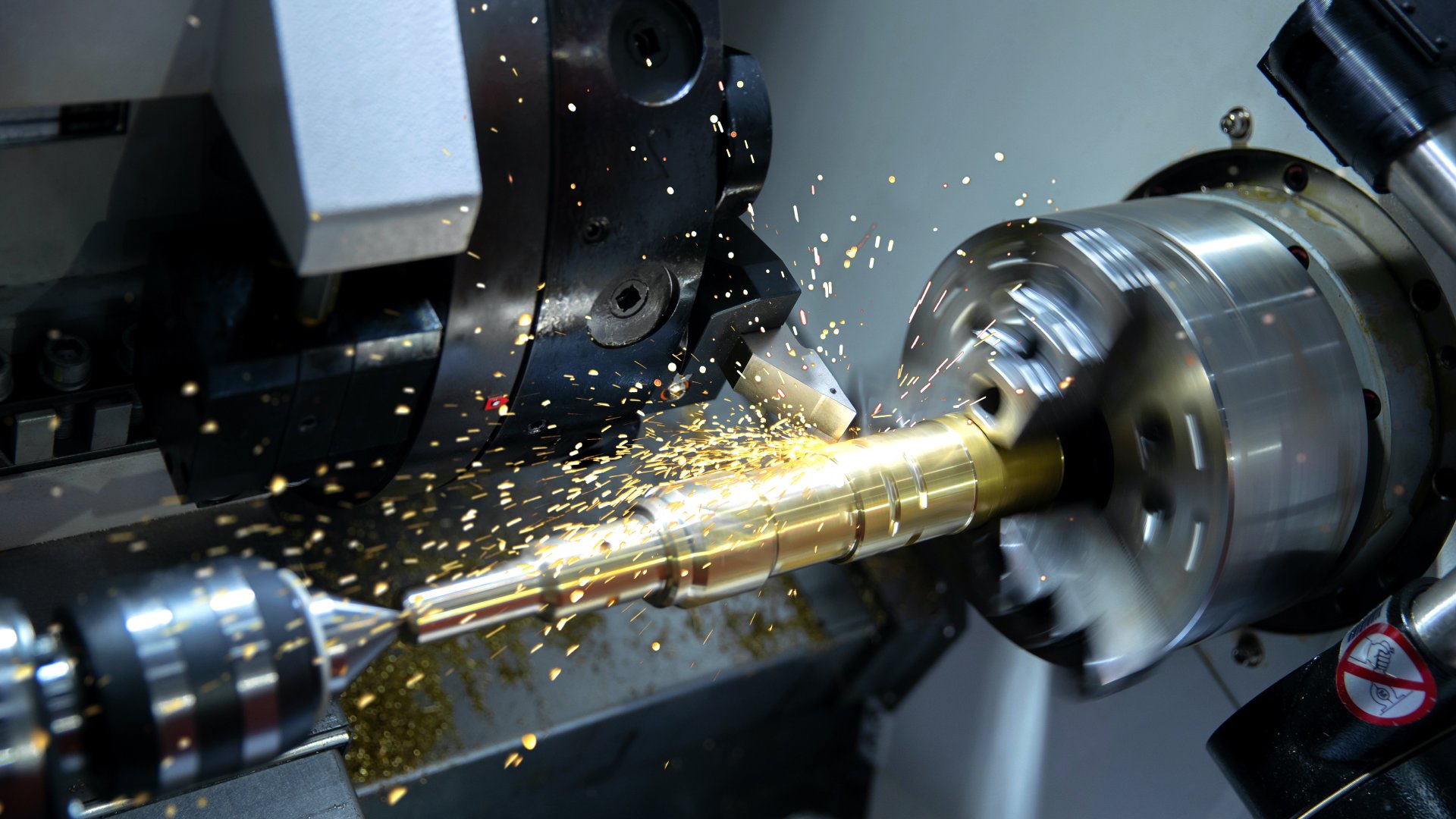
Whether you’re cutting metals or working with composites, high-speed machining allows you to work with speed, precision, and efficiency. Knowing how it works and what makes it so effective can set you up for success. In this guide, we’ll break down what you need to know about high-speed machining.
The Difference High-Speed Machining Makes
Unlike traditional machining, high-speed methods create smaller chips and generate less heat. Heat control matters here because it minimizes wear on your tools. High-speed machining requires you to find the right spot between speed, feed rate, and depth of cut to lower machining time while preserving tool life.
For example, aluminum responds wonderfully to high-speed machining due to its high thermal conductivity, making it easier to manage heat buildup. Getting these basics right and following high-speed machining best practices for tooling lays the foundation for consistent and efficient results.
Why Tooling Is Important
The right tools enable you to handle higher cutting speeds without compromising quality. Carbide tools, which are known for their hardness and heat resistance, are popular for these applications. However, carbide tools have their limits. Coatings such as titanium aluminum nitride (TiAlN) can boost heat resistance and extend tool life.
Differences in Material Types
Another thing you need to know about high-speed machining is that it requires you to tailor your techniques to suit specific materials. Metals, polymers, and composites each react differently to high-speed cuts. For example, titanium benefits from lower feed rates due to its strength, yet it works well with thermal conductivity-focused tools. On the other hand, softer metals such as aluminum allow faster cuts and longer tool life. Knowing these differences ensures your machining efforts align with your chosen material’s unique properties.
Achieving Precise Programming
CNC programming plays an essential role in high-speed machining. In particular, creating efficient toolpaths influences surface quality and production time. Strategies such as trochoidal milling, which uses smaller, faster circular cuts, reduce stress on tools and lower heat generation. Even small adjustments in your code to optimize entry and exit points impact performance. You don’t need to be an expert coder to implement this either; user-friendly CAM software simplifies the process.
Modern CNC machines built for high speeds also handle sharper accelerations and decelerations with ease. Rigid machine structures reduce chatter, ensuring smooth finishes on your parts. Upgrading equipment or retrofitting older machines with modern components enhances performance when high-speed machining drives your operations.
The Importance of Coolant Systems
High-speed machining generates significant heat. Proper cooling prevents tools from wearing out quickly and keeps surface finishes in top shape. Modern coolant delivery systems, including through-spindle coolant, target cooling exactly where it’s needed.
For example, when machining steel, effective coolant dispersal helps control temperature and prevent thermal expansion. Coolant also clears chips from the cutting zone, reducing re-cutting and improving part quality.