Understanding the Components of a Tracked Undercarriage
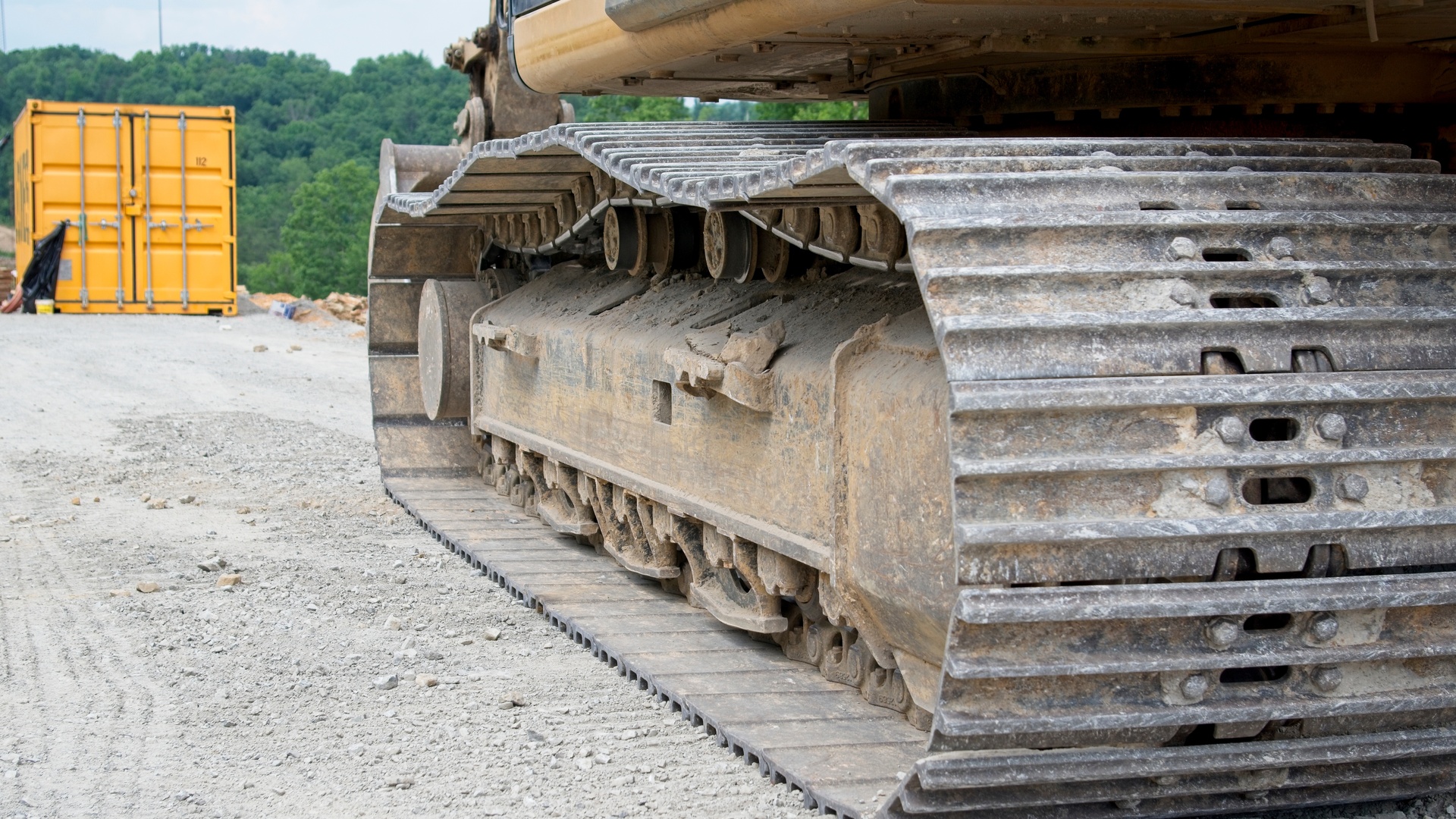
When it comes to heavy machinery, understanding the components of a tracked undercarriage can feel like unlocking a hidden secret to efficiency and durability. Whether you're an equipment operator or simply someone fascinated by powerful machines, knowing how these parts work together adds a whole new appreciation for the engineering behind them. Let's pull back the curtain and break down the key components that make tracked undercarriages essential for stability, traction, and performance.
The Role of Tracks
At the heart of any tracked undercarriage is the track system. Tracks are the workhorses that provide the stability and traction to keep machinery moving over challenging terrain like loose dirt, mud, or rocks. They evenly distribute the equipment's weight, preventing machines from sinking into soft ground.
Tracks come in two main varieties—rubber and steel. Rubber tracks are used for lighter, more versatile machines like compact track loaders, offering flexibility and reduced ground damage. Steel tracks, on the other hand, dominate when it comes to heavy-duty equipment like excavators, providing maximum durability and support.
The Undercarriage Frame
The undercarriage frame is the structure that connects all the other components. Designed to endure tough working conditions, the frame safeguards crucial internal parts from damage. Manufacturers design these frames with resilience in mind, using high-strength materials to withstand the constant wear and tear of demanding tasks. Without a strong frame holding the system together, the efficiency of the whole machine would take a hit.
Rollers and Their Purpose
Rollers are the unsung heroes that keep everything running smoothly. Located on both the upper and lower sections of the undercarriage, these cylindrical components minimize friction and ensure the track moves consistently and efficiently. Bottom rollers distribute the machine’s weight across the tracks, preventing the system from collapsing under pressure. Top rollers, meanwhile, keep the track aligned, reducing sagging and ensuring steady movement. Functioning rollers provide better balance and longer-lasting tracks, which translates to smoother operation.
Importance of Sprockets and Idlers
Sprockets and idlers are key components in tracked heavy equipment. The role of sprockets in undercarriage performance is a critical one. Sprockets transfer the engine power to the tracks, which propel the machine forward. Meanwhile, idlers play a supporting role by maintaining the proper tension in the tracks. This prevents slack and ensures the tracks maintain firm contact with the rollers and the ground. When sprockets and idlers work in sync, they provide seamless movement and efficient operation.
Understanding the components of a tracked undercarriage sheds light on the incredible engineering behind heavy machinery. From the strength of the frame to the precision of the sprockets and idlers, every part has its role in delivering smooth, efficient performance. Appreciate the mechanisms at play, and your machines will serve you well.