6 Best Practices for Measurement Accuracy in Fabrication
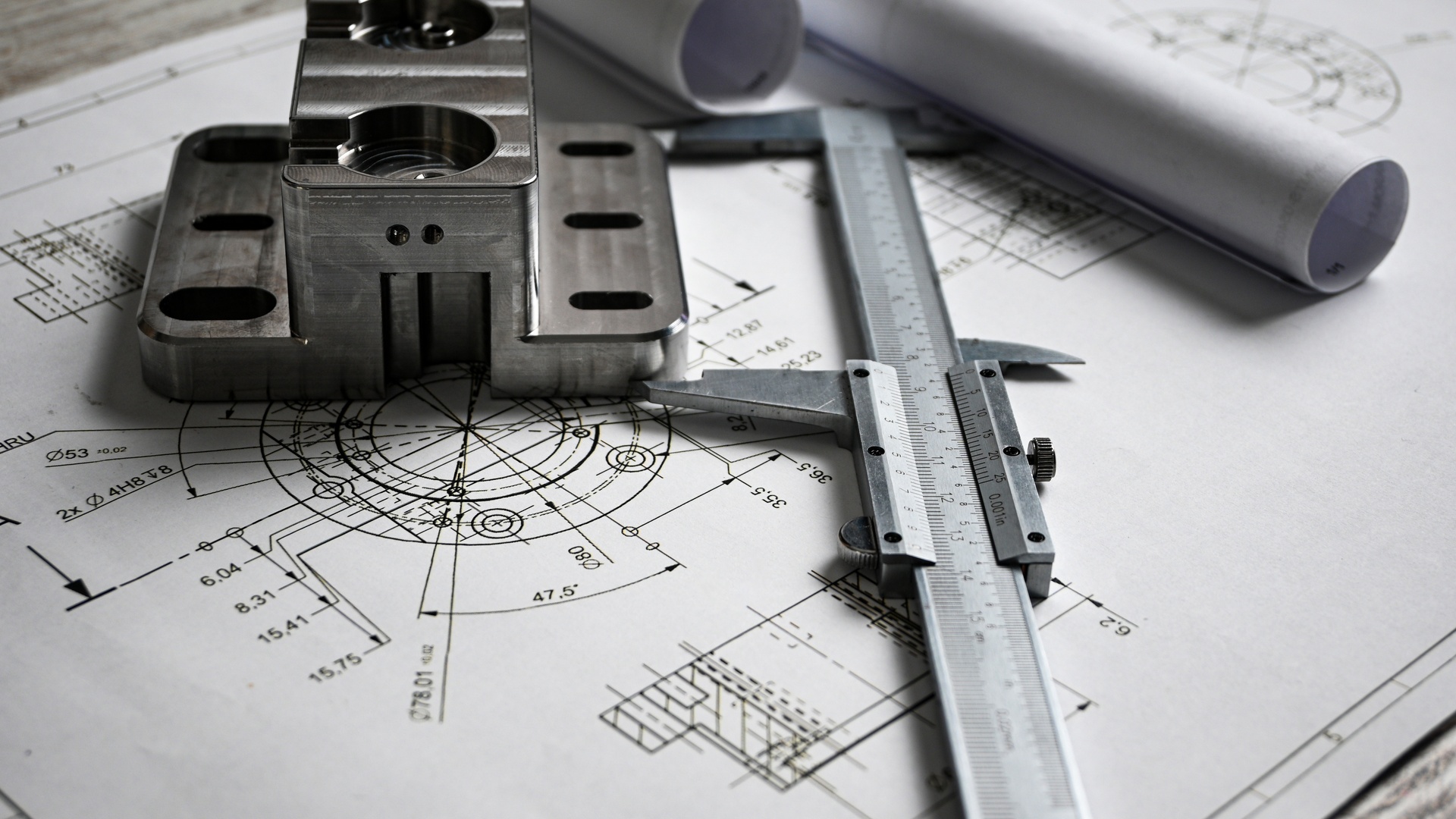
When it comes to fabrication, precision is everything. But beyond the usual advice of “measure twice, cut once,” there are deeper, industry-specific practices that help ensure true accuracy.
In Northeast Wyoming and Southwest South Dakota, temperatures swing, and materials vary, so mastering these six best practices for measurement accuracy in fabrication will help you go beyond the basics.
1. Account for Material Expansion and Contraction
Metals expand and contract in response to temperature changes, which is especially important in regions with fluctuating weather conditions. Measuring a steel plate on a cold morning and cutting it mid-afternoon when it’s warmer will cause fit issues.
Take environmental factors into account by measuring materials at temperatures close to those at which fabrication will occur. This small step can prevent costly adjustments later.
2. Calibrate Tools for Specific Materials
Not all metals are created equal, and neither are their measurement needs. For example, measuring a thin aluminum sheet requires a different approach than a thick steel beam.
Calibrate your measuring devices before each major project or whenever you switch to a different material type. Some materials may need more frequent calibration to maintain accuracy, especially in fabrication environments where precision tolerances are tight.
3. Factor in Weld Bead Allowances
A common pitfall is forgetting to account for the size and penetration of weld beads. Weld beads add thickness or alter dimensions subtly but significantly.
This practice will help you understand the true costs of welding defects, as overlooking bead size can lead to rework or structural issues.
4. Use Templates and Jigs for Repetitive Tasks
When fabricating multiple identical parts, custom templates or jigs become invaluable. They provide a consistent reference point for measurements and cuts, reducing human error and increasing production efficiency.
Whether you’re building railings or machine components, these tools help maintain tight tolerances across every piece.
5. Measure from Multiple Reference Points
Relying on a single measurement point allows small errors to compound, particularly on larger or more complex assemblies. Double-check measurements by cross-referencing from different points.
Doing so will catch any inconsistencies early and keep your parts fitting together perfectly.
6. Factor in Surface Finish and Machining Tolerances
Precision isn’t just about raw measurements. Surface finishes, machining allowances, and fitting tolerances all influence how parts come together.
Allow for these variables by consulting machining specs and planning accordingly. This helps make sure your fabricated pieces measure correctly and function properly once assembled.
Foster a Culture of Precision
Beyond tools and techniques, the best fabrication shops cultivate an environment where accuracy matters at every step. Encourage team members to communicate openly about measurement uncertainties, maintain equipment diligently, and pause to verify critical dimensions. Good mindsets prevent errors before they occur and make sure that projects flow smoothly.
Mastering these six best practices for measurement accuracy in fabrication can transform how your shop handles projects. Taking extra care to adapt to materials, environment, and workflow nuances keeps quality high and costs low, no matter where your fabrication takes place.